Правообладателям!
Представленный фрагмент книги размещен по согласованию с распространителем легального контента ООО "ЛитРес" (не более 20% исходного текста). Если вы считаете, что размещение материала нарушает ваши или чьи-либо права, то сообщите нам об этом.Читателям!
Оплатили, но не знаете что делать дальше?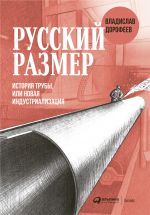
Текст бизнес-книги "Русский размер"
Автор книги: Владислав Дорофеев
Раздел: О бизнесе популярно, Бизнес-книги
Возрастные ограничения: +12
Текущая страница: 3 (всего у книги 3 страниц)
Главное – не суетиться. ТЭСЦ-4
В административном корпусе трубоэлектросварочного цеха № 4 (ТЭСЦ-4) лестничные ступени – из стали. Сталь здесь – не декор и не элемент дизайна, сталь на заводе – это суть, смысл, нутро. Трубное сердце ВМЗ. Оно стальное и умное. Здесь производят знаменитые выксунские трубы большого диаметра (ТБД, до 1420 мм), самые круглые и самые гладкие изнутри, что экономит 10–15 % средств при прокладке трубопроводов, а затем при перекачке энергоресурсов (газ, нефть). Цена аренды судна-трубоукладчика доходит до 1 млн долл. в сутки, сухопутного трубоукладчика – до 100 000 долл. Это означает экономию в десятки и сотни миллионов рублей, что превращает выксунские трубы в самые эффективные в мире, продаваемые по рыночным ценам.
Цех – лидер по безопасности труда на ВМЗ-2018, о чем свидетельствует награда – золотая каска с золотым же лавровым венком.
Евгений Залетин, начальник цеха ТЭСЦ-4, наголо бритый. Говорят, его любят рабочие. Застал его за составлением ежегодного отчета-2018 и презентации-2019. Презентации и отчеты ввел еще бывший директор ВМЗ Сергей Филиппов. Трудно было сделать только первую презентацию, дальше – легче. «Про Филиппова недоброжелатели говорили, что Филиппову делать нечего, ходит, ищет окурки. Но с этих окурков началась новая история завода».
В ТЭСЦ-4 работает около 1500 человек. Там выпускают трубы 15 диаметров и с толщиной стенки 8–43 мм. Двенадцать диаметров на линии-1020, еще три – на линии-1420. Максимальная длина трубы– 12,2 м. На линии-1020 используется технология U-формовки трубы, на линии-1420 – пошаговая JCOE[3]3
JCOE – процесс формовки сварных труб большого диаметра, состоящий из стадий J-образной, С-образной и О-образный формы профиля. – Прим. ред.
[Закрыть]. Линия-1020 запущена в 1992 г., на ней нельзя сделать трубу с толщиной стенки более 30 мм. Зато производительность на линии-1020 почти вдвое выше, чем на линии-1420. На линии-1020 план в сутки составляет 500 труб (около 7 000 т), план месяца – 50 000 т. Линия-1420 запущена в 2005 г. Линия-1420 сейчас работает два дня через два. Линия-1020 работает круглосуточно, постоянно. За последние 10 лет цех произвел 10,6 млн т ТБД. В 2018–2019 гг. наблюдается самое большое падение заказов на ТБД за 10 лет, до 700 000–800 000 т в год. Критическая граница – 500 000 т в год.

Трубоэлектросварочный цех № 4 – трубное сердце ВМЗ. Оно стальное и умное. Здесь уверены: чтобы производить лучшие в мире трубы большого диаметра для трансконтинентальных трубопроводов, надо прежде хотеть этого.
Первый мой проводник – Алексей Крошкин, начальник смены, в его смене 250–300 человек.
Задача Крошкина – план и люди, то есть продукция и безопасность. Он из первого набора выксунского филиала МИСиСа, 1997 г. Начальником смены работает пять лет, до этого 10 лет был мастером.
По словам Крошкина, заказы еще год назад упали до 30–40 % загрузки мощностей. Но сейчас идет подъем и людей возвращают из других подразделений.
В операторской кабинке на линии формовки ТБД – три оператора, три вершителя судьбы трубы. Они главные, в их руках металл становится послушным. Это надо видеть, об этом надо знать. Удивительная сила преобразования бессмысленной материи в осмысленный порядок, аморфного и бесформенного материала – в осмысленный продукт посредством осмысленного труда.
Звук сгибаемого в трубу листа – это могучий утробный стон и хруст. Сотрясается огромная махина пресса. Кажется, что пространство вокруг приходит в движение. Прощай, вольница. Будто сама природа сопротивляется натиску пресса. Хаос на моих глазах превращается в космического уровня продукт. Похоже, что оборудование скрипит, трещит, работает из последних сил – как и люди. Но люди могут уйти в отпуск, отдохнуть. А оборудование работает круглосуточно, останавливаясь только на профилактические и текущие ремонты и осмотры.
После формовки трубы – замер размеров.
Тотальный контроль по всей цепочке производства трубы, 15 точек автоматического и ручного контроля. В результате выход трубы – 98,7–99,8 %. Для проекта «Турецкий поток» выход был 99,998 %, это означает минимальный брак. За последние пять лет брак в цехе снизился в разы.
Идеальный выксунский круг проверяют с помощью СОП (стандартный образец предприятия) – это своеобразный камертон трубы, в который входит набор калибраторов, специальных лекал с полуокружностями и ручные дефектоскопы, которые осуществляют ручной ультразвуковой контроль (РУЗК) готовой трубы. Есть шкаф с полками, на которых лежат десятки калибраторов круга, библиотека камертонов-калибраторов, она же калибровочная или камертональная библиотека.
А еще есть склад образцов-камертонов – это реальные трубы с разными диаметрами и толщиной стенки. Это лекала, по которым калибруется РУЗК сварного шва. И есть набор труб с заданными дефектами.
Неожиданно вернули трубу с РУЗК. Сразу собралась рабочая группа из представителей разных подразделений, которые делали трубу, чтобы решить, что делать с трубой – на переплавку или в доработку.
Крошкин поясняет происшедшее: наш девиз – не отдать на следующий этап бракованную трубу. Следующий участок выступает как заказчик по отношению к предыдущему.
Для Алексея Крошкина производственная система разбила историю завода на время «до» и «после» внедрения ПС. На страхе долго не протянешь, поэтому внедрение ПС держалось на мотивирующих и стимулирующих факторах, а также на безопасности и чистоте. В процессе внедрения и освоения ПС люди менялись, осознавая, что ПС – это реальная забота о них.
По мнению Крошкина, производственные системы – это прежде всего здравый смысл. Во всех направлениях, во всех делах, во всем. И это здесь самое распространенное суждение о ПС.
До внедрения ПС на заводе многое было «на живую нитку». ПС привнесла системный подход во все звенья и направления производства. ПС сделала жизнь рабочего человека на заводе лучше. Отремонтированы все бытовые помещения, все туалеты. Рабочим предоставляется все необходимое – лишь бы работали. Появился ощутимый эффект, отдача.
Прошедшие годы изменили завод на глазах Крошкина. 15 лет назад не было крыши над пролетом погрузки труб в вагоны, и люди жгли костры, чтобы согреться. Теперь здесь тепло, светло и сухо, есть и крыша над головой, и окна. На каждый сортамент труб своя схема погрузки в вагоны.
По мнению Крошкина, программа ТОП-2 (корпоративная программа «Тотальная оптимизация производства-2»), стартовавшая в конце 2018 года, призвана выполнить ту же задачу, что и предыдущая «Тотальная оптимизация производства» (ТОП-1), реализованная в начале 2000-х, – способствовать росту производительности труда и высвободить примерно пятую часть специалистов на основных производствах, чтобы направить их на новые производства, которые сейчас строятся на ВМЗ.
Крошкин подал документы на включение в программу ТОП-2, чтобы попасть в число навигаторов, которые будут реализовать на местах задачи ТОП-2 и потом войдут в кадровый резерв высшего руководящего состава завода.
Личные мотивы Алексея Крошкина в его работе на заводе: трудится по специальности и востребован; ВМЗ – знак и символ надежности, стабильности, перспектив, самая высокая зарплата в Выксе; хочет продолжить карьеру и пойти по служебной лестнице, потому что на заводе есть все возможности для роста и развития. А он не боится принимать решения, потому что, если боишься ответственности и последствий, надо сидеть в своей скорлупе.
Линию формовки труб остановили для перевалки и перенастройки на новые параметры трубы по новому контракту для нового заказчика. К работе приступила бригада перевальщиков. У наладчика – особая служба. В любое время могут вызвать из дома – даже не выпьешь, потому что всегда можешь быть востребован, если не в отпуске. Даже в выходной, если дежурная бригада не справляется. Как на «скорой помощи».
С утра делали партию ТБД с толщиной стенки 10 мм, затем после перевалки (то есть переналадки) выпустили только одну трубу большого диаметра с толщиной стенки 9 мм. Труба по себестоимости получилась «золотая». Но таков заказ, покупателю нужна была всего одна труба с соответствующими характеристиками.
Мой новый проводник Вадим Наумов – и. о. начальника смены, мастер участка отделки. Закончил МИСиС, учился в 2004–2010 гг. платно, платил ежегодно 20 000 руб. Идем по цеху.
Вадим Наумов на заводе с 2003 г. На своем участке он может все, заменит любого – у него пять специальностей, четыре рабочих и одна инженерная. По всем специальностям прошел обучение, сертифицирован, ежегодно сдает экзамены, подтверждающие право на работу. И он не один такой. В ТЭСЦ-4 люди должны быть взаимозаменяемыми. Не хочешь – не учись, но поднимается по служебной лестнице и в зарплате тот, кто имеет несколько специальностей. А на одном станке можно до пенсии просидеть.
Удивительные на заводе встречаются люди. Навстречу с окладистой черной бородой, коренастый, крепкий, среднего роста – будто ополченец из дружины нижегородцев, купца Кузьмы Минина и князя Дмитрия Пожарского, только кольчугу зачем-то снял и меч с булавой припрятал до поры.
В цехе, как и на заводе, выдают крем для рук, перчатки, стирают и штопают спецодежду. Вижу барышню без перчаток. Почему? «Жарко в них!»
Марина Шибанова, сортировщик-сдатчик, в цехе 33 года, пришла на производство в 1986 г. Хотела после техникума устроиться в котельную, но там не взяли. Наверное, тогда туда брали «по блату». В ее работе надо много знать, чтобы добиться результата. Все начинается с задачи – диаметр и характеристики трубы. Затем назначается «разведчик» – вырезается образец трубы; так по каждой партии, чтобы потом проверить состав и характеристики металла, которые могли измениться после формирования трубы.
Татьяна Кикеева, сортировщик-сдатчик. Работает с 2008 г. Перед заступлением на должность окончила 10-дневные курсы, сдала экзамены и вот уже 10 лет успешно работает. Когда она или ее напарница уходят в отпуск, их могут заменить обученные работники с других участков.
В какой-то момент эстафету проводника перехватит Кирилл Кудряшов, и. о. сменного мастера участка формовки. Закончил выксунский филиал МИСиС в 2016 г. – тоже платно, уже за 48 000 руб. в год.
Теперь завод оплачивает учебу мастерам, которые заочно получают высшее образование. А мои проводники платили самостоятельно.
Кирилл Кудряшов: «Ночью, конечно, тяжелее, чем днем. Но в задании не учитываются ни мера усилий, которые надо приложить, чтобы выпустить трубу, ни время суток, ни твое состояние и т. п. Все это не имеет значения».
Александр Ласанкин – оператор пресса предварительной формовки. В цехе работает 20 лет, 16 лет на прессах, четыре года на сварке. Пресс формовки трубы – это сердце цеха. В ТЭСЦ-4 два сердца, на линии-1020 и линии-1420. Сердце-1020 – пресс 57, пресс формовки труб диаметром до 1020 мм. Три раза за смены проверяют параметры настройки линии.
Конечно, это не панацея. На моих глаза застряла заготовка трубы в прессе формовки трубы на линии-1020. Вся линия остановилась по цепочке в обе стороны от пресса. Это зона ответственности Василия Жукова, бригадира-настройщика, жилистого, невысокого. Поначалу заметался у пресса, отключил истошный звук сработавшего клапана. Дернулся к прессу, в зону формовки, но остановился в сомнениях. Видно было, какое он переживал сильнейшее внутреннее напряжение – вызов, который грозил остановкой линии, выходом из графика, рухнувшим планом смены и цеха. И видно было, как он справился с внутренней паникой и буквально на глазах преобразился.
Я стоял совсем рядом. Нерешительность и суматошность сменились на уверенность и ясность. Это напряжение вызывало уважение и радость, какую вызывает человек, который думает, анализирует реальность и ситуацию, в которой он оказался, когда от его решения зависит цех и больше – завод. Похоже, он понял причину затора. Он вышел из зоны формовки, остановился… И линия на наших глазах заработала. Хотя после отключения аварийной кнопки клапана больше ничего бригадир не трогал. Судя по реакции, он этого и ожидал. Он знал, он понял, что линия сейчас заработает.
Разумеется, потом он все объяснил. Это была первая заготовка для первой трубы в новой серии после перевалки – пошел новый лист из нового металла, заготовка из которого ведет себя иначе, чем в предыдущей серии. Бригадир разобрался в причине остановки, опираясь на опыт, знания, кругозор. Он взял на себя ответственность, смелость выйти из зоны комфорта. Принял решение, от которого зависит план цеха и премия нескольких сотен человек. Вся эта сцена заняла несколько секунд – вы мое описание дольше читаете. Но это был высочайший градус напряжения. Бригадир в эти секунды находился на пределе усилий, и это напряжение далось ему крайне нелегко – на лице кожу буквально стянуло. На руках и на шее буквально жилы выступили. Жуков пережил состояние сильнейшего нервного и физического напряжения. Когда он подошел ко мне, по его лицу ручьем стекал пот. Но глаза! Глаза веселые! Ни паники, ни страха. Да! Итог, вывод, оценка своих действий, внутренний рецепт: главное – не делать лишних движений, не суетиться. После этой показательной истории иначе воспринимаются слова Кирилла Кудряшова: «Везде у нас тут смертельно опасно. И просто опасно». Он имел в виду и человеческую безопасность, и экономическую.
Жуков здесь не один такой. Отпечаток этой тяжелой, выматывающей работы на всем – на лицах, на фигурах, на руках, в движениях, в мимике (или в ее полном отсутствии, когда уже нет сил). Все и всегда происходит при максимальном напряжении сил. Трубное производство – это пятый передел, голубая кость черной металлургии. Но как же трудно это дается! Огромное число людей. Каждая труба – это невероятные усилия. И этих труб десятки и сотни тысяч.
Василий Жуков на заводе уже 39 лет. В ТЭСЦ-4 пришел еще на стадии строительства цеха. Так и работает на участке формовки. Ему 61 год – но силы пока есть. Предполагает еще лет пять отработать. Впрочем, как здоровья хватит. «Какую заготовку мы сделаем, такой будет труба, – говорит он. – Конечно, за 39 лет завод изменился. Чистота и порядок теперь. Приятно пройти. Говорят же, хорошую вещь в сарае не сделаешь. Тяжело, когда суетишься, когда делаешь много лишних движений». И вновь повторил, акцентировал: «Главное, не делать лишних движений, не суетиться. Один человек может из-за необдуманного решения остановить или тормознуть весь цех. Перенастраиваемся под каждую марку стали, под каждого поставщика».
У него в бригаде не было случая, чтобы человек отказывался осваивать вспомогательные и смежные профессии. Он сам умеет в своей бригаде все делать, каждого может заменить, но для этого ежегодно он сдает пять экзаменов по пяти специальностям, подтверждая профессиональную компетентность. «Например, все работники цеха ежегодно обязательно сдают экзамен на стропальщика. От человека, который откажется осваивать смежные специальности, надо избавляться, потому что такой человек будет тупо сидеть до пенсии на своем месте. У меня всю жизнь в голове порядок. Я всю жизнь так живу. Потому когда внедрили производственную систему, я это воспринял как должное, как дополнительные, но необходимые требования. В моей бригаде нет текучки».
Участок ремонта труб и сварки – в совместном управлении Виктора Шеваренкова и Марии Степановой. Здесь отыскивают задиры на трубах, капли от сварки и т. п.
Виктор Шеваренков – сменный мастер участка. На завод пришел после армии в 1991 г., отработал уже 28 лет. У него всегда была установка: варить «с головой». Сейчас заочно учится в выксунском филиале МИСиС. Он осваивал линию-1020, а затем линию-1420. На линии-1020 сварочное оборудование еще специалисты из киевского института Патона налаживали. Был сварщиком, когда выпускали трубы для проектов «Сахалин-1», «Сахалин-2», «Северный поток – 1» и «Северный поток – 2» – сварка под флюсом. Уже на «Северном потоке – 1» не курили и не выпивали на рабочем месте. Все, кто работал на проектах, прошли аттестацию. Теперь на его участке все сварщики имеют 6-й разряд. На каждом участке все должно соответствовать стандартам – теперь даже сварная проволока приходит в специальных пакетах.
«Сахалин-1» – нефтегазовый проект, реализуемый на острове Сахалин по условиям соглашения о разделе продукции (СРП) с 1996 г. Объем извлекаемых запасов оценивается в 2,3 млрд баррелей нефти (307 млн т) и 485 млрд м³ природного газа. Жизненный цикл проекта – до 2040–2050 гг. Оператор проекта – «Эксон Нефтегаз Лимитед», дочерняя компания ExxonMobil (30 %), другие акционеры – ОАО «Роснефть» (20 %), ONGC (20 %) и SODECO (30 %). Проект «Сахалин-1» остается одним из крупнейших проектов с прямыми иностранными инвестициями в России.
«Сахалин-2» – нефтегазовый проект, реализуемый на острове Сахалин на условиях соглашения о разделе продукции с 1996 г. Оператор проекта компания «Сахалин Энерджи». Общие запасы – 182,4 млн т нефти и 633,6 млрд м³ газа (по другим данным – 150 млн т нефти и 500 млрд м3 газа). В 2009 г. в рамках проекта начал работу первый в России завод по производству сжиженного природного газа. В 2014 г. выведена на мировой рынок легкая малосернистая нефть сорта «Сахалин Бленд». Акционеры: «Газпром» (50 % плюс одна акция), Shell (27,5 % минус 1 акция), Mitsui (12,5 %), Mitsubishi (10 %).
«Северный поток» (англ. Nord Stream, ранее – морская часть Северо-Европейского газопровода) – газопровод между Россией и Германией, проходящий по дну Балтийского моря. Является морской частью одной из веток системы газопроводов «Ямал – Европа». Помимо «Северного потока», в ветку входит газопровод «Грязовец – Выборг» в России и газопроводы OPAL и NEL в Германии. Участники проекта – Россия, Германия, Нидерланды и Франция. Основная цель – снижение зависимости от транзитных стран. Прокладка трубопровода начата в апреле 2010 г. В сентябре 2011 г. начато заполнение технологическим газом первой из двух ниток. 8 ноября 2011 г. начались поставки газа по первой нитке газопровода. 18 апреля 2012 г. была закончена вторая нитка. 8 октября 2012 г. начались поставки газа по двум ниткам газопровода в коммерческом режиме. На маршруте газопровода «Северный поток – 1» – самый длинный подводный маршрут экспорта газа в мире, его протяженность – 1224 км. Владелец и оператор – швейцарская компания Nord Stream AG, созданная в 2005 г. для управления проектом «Северный поток – 1», штаб-квартира располагается в швейцарском городе Цуг; среди учредителей – «Газпром» и экс-канцлер Германии Герхард Шредер.
Александр Пичугин – дефектоскопист. На участке с 2016 г. Заочно окончил МИСиС. Прекрасно понимает физику всех рабочих процессов и каждый год проходит врачебный осмотр глаз. Его очень радует то, что он работает, возможно, в лучшем в мире цехе ТБД – радует не меньше, чем заказы и премии.
Контроль сварного шва трубы СНК (средствами неразрушающего контроля) производится, например, с помощью РТК (рентген-телевизионный контроль) шва. Допускаемый дефект инородного включения в сварном шве трубы – до 3,2 мм. Никто не знает, откуда берутся эти инородные включения, но в целом все стандартизировано. Мария Степанова: «У нас тут чудес не бывает. Чудеса остаются за проходной! Хотя бывает, случаются странности, один датчик, например, время от времени не срабатывает, а затем вновь работает. Его заменяют, и новый тоже не срабатывает, а потом опять нормально работает».
Внимание! Это ознакомительный фрагмент книги.
Если начало книги вам понравилось, то полную версию можно приобрести у нашего партнёра - распространителя легального контента ООО "ЛитРес".Правообладателям!
Представленный фрагмент книги размещен по согласованию с распространителем легального контента ООО "ЛитРес" (не более 20% исходного текста). Если вы считаете, что размещение материала нарушает ваши или чьи-либо права, то сообщите нам об этом.Читателям!
Оплатили, но не знаете что делать дальше?